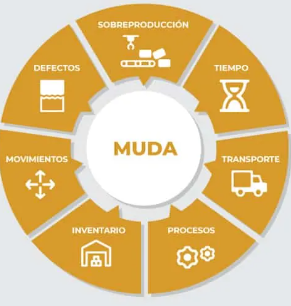
¡Hola, lectores apasionados por la eficiencia y la mejora continua! Hoy nos sumergiremos en el fascinante mundo de la metodología Lean, una filosofía que ha revolucionado la forma en que las empresas abordan la producción y la gestión. ¿El objetivo? Deshacernos de cualquier cosa que no aporte valor y, por supuesto, optimizar todo el proceso. ¡Es hora de hablar sobre los 7 Mudas de Lean y cómo eliminarlos para alcanzar la excelencia operativa!
¿Qué es Lean?
Primero, dejemos en claro qué significa ser Lean. En pocas palabras, es un enfoque que busca eliminar desperdicios y maximizar el valor para el cliente. Se trata de hacer más con menos, reduciendo costos, tiempos de entrega y, lo más importante, centrando cada acción en lo que realmente importa.
Por otra parte, «Muda» es una palabra japonesa que, en el contexto de la metodología Lean, se traduce comúnmente como «desperdicio» o «despilfarro». Cuando nos referimos a los «7 Mudas de Lean», estamos hablando de los siete tipos de desperdicios que la metodología Lean busca identificar y eliminar en un proceso empresarial. La idea central es reducir o eliminar estos desperdicios para mejorar la eficiencia y agregar más valor al cliente. ¡Así que, eliminemos esos «mudas» y hagamos nuestros procesos más eficientes!
Los 7 Mudas de Lean: Un Vistazo Rápido
Ahora, hablemos de los siete pecados capitales del Lean, también conocidos como los «7 Mudas». Estos son los enemigos a vencer para lograr la perfección en la producción:
- Sobreproducción: ¡Menos es más! No queremos producir más de lo necesario porque eso genera costos adicionales y acumula inventario innecesario. Un ejemplo podría ser fabricar demasiados productos antes de que la demanda real se manifieste.
- Inventario: Hablando de inventario, es como el exceso de peso en una dieta. Mantén solo lo esencial. El inventario excesivo no solo ocupa espacio, sino que también atesora capital que podría invertirse de manera más efectiva en otros aspectos del negocio.
- Defectos: Aquí hablamos de productos defectuosos o servicios que no cumplen con los estándares de calidad. ¡Nada de productos ‘meh’! Los defectos generan retrabajo, desperdician tiempo y, por supuesto, afectan la satisfacción del cliente.
- Transporte: La idea es simple: cuanto menos movimiento, mejor. Cada vez que trasladamos algo, ya sea física o virtualmente, estamos gastando recursos. Reduce el transporte innecesario y optimiza tus rutas.
- Sobreproceso: No queremos hacer más trabajo del necesario. Centrémonos en lo que realmente agrega valor. Si estás llenando informes solo porque siempre se han llenado, es momento de replantearse el proceso.
- Espera: El tiempo es dinero, y esperar es como tirar dinero por el desagüe. Ya sea esperar por materiales, aprobaciones o cualquier cosa que retrase el proceso, ¡eso es un Muda!
- Movimiento: Minimizar el movimiento innecesario es crucial. Cada paso, cada movimiento, debe ser esencial para la tarea en cuestión. No queremos a nuestros empleados dando vueltas como pollos sin cabeza.
Identificar Desperdicios: Señales y
Identificar los desperdicios, o «mudas», en un proceso empresarial es esencial para aplicar con éxito la metodología Lean. Aquí hay una guía práctica para reconocer estos desperdicios:
- Sobreproducción:
- Señales: Exceso de inventario, largos tiempos de espera, productos almacenados sin demanda.
- Cómo Identificar: Compara la producción con la demanda real. ¿Estás fabricando más de lo que se necesita? ¿Hay un exceso de productos en stock?
- Inventario:
- Señales: Almacenes llenos, productos obsoletos, dificultad para rastrear y gestionar inventario.
- Cómo Identificar: Evalúa la rotación del inventario y la necesidad real de mantener ciertos productos en stock. ¿Hay elementos que podrían producirse o adquirirse según sea necesario?
- Defectos:
- Señales: Reclamaciones de clientes, retrabajo frecuente, costos adicionales de garantía.
- Cómo Identificar: Realiza un seguimiento de los productos defectuosos. ¿Necesitas corregir errores con frecuencia? ¿Los clientes reportan problemas con tus productos o servicios?
- Transporte:
- Señales: Movimientos excesivos de materiales, largas distancias de transporte, demoras en la entrega.
- Cómo Identificar: Analiza la eficiencia de tus rutas de transporte y evalúa si puedes reducir distancias o consolidar envíos para minimizar movimientos innecesarios.
- Sobreproceso:
- Señales: Pasos en el proceso que no agregan valor, tareas duplicadas, procesos complejos y redundantes.
- Cómo Identificar: Examina cada paso del proceso y pregunta si agrega valor al producto o servicio. ¿Existen pasos que podrían eliminarse sin afectar la calidad final?
- Espera:
- Señales: Tiempos muertos, empleados inactivos, procesos que esperan aprobaciones.
- Cómo Identificar: Rastrea los tiempos de espera en cada fase del proceso. ¿Los empleados o las máquinas están inactivos debido a la espera de algo?
- Movimiento:
- Señales: Movimientos innecesarios de empleados, búsqueda constante de herramientas o materiales.
- Cómo Identificar: Observa el flujo de trabajo. ¿Los empleados se desplazan más de lo necesario? ¿Hay una organización eficiente de herramientas y materiales?
Eliminar Desperdicios: Un Paso a la Vez
Ahora que conocemos a nuestros enemigos, hablemos de cómo derrotarlos. La eliminación de desperdicios no es un proceso de un solo golpe, sino un compromiso constante con la mejora. Aquí hay algunas estrategias prácticas para deshacernos de cada Muda:
- Sobreproducción: Producción Justo a Tiempo (JIT) La clave aquí es producir lo necesario en el momento adecuado. Implementar el JIT implica ajustar la producción según la demanda real, evitando así el exceso de inventario y reduciendo costos de almacenamiento. Esto no solo mejora la eficiencia, sino que también responde directamente a las necesidades del cliente.
- Inventario: Kanban y Sistema Pull Introduce el método Kanban para visualizar y gestionar tu inventario de manera eficiente. Además, implementa un sistema Pull, donde la producción comienza solo cuando hay una demanda real. Esto asegura que el inventario se mantenga bajo control y que solo se produzca lo necesario.
- Defectos: Sistema Poka-Yoke La prevención de defectos es clave. Implementa sistemas Poka-Yoke, que son mecanismos a prueba de errores para evitar la creación de productos defectuosos. Esto reduce los retrabajos y garantiza una calidad constante.
- Transporte: Diseño de Flujo Continuo Simplifica tu proceso de producción y reduce al mínimo el transporte. Adopta el flujo continuo, donde las tareas se realizan de manera secuencial y sin interrupciones, eliminando la necesidad de mover productos o información de un lugar a otro.
- Sobreproceso: Valor Agregado vs. No Agregado Analiza cada paso en tu proceso y pregunta: ¿esto agrega valor al cliente? Si la respuesta es no, ¡elimínalo! Centrémonos en lo que realmente importa para el cliente y eliminemos las actividades superfluas.
- Espera: Sincronización de Procesos Optimiza los tiempos de espera sincronizando los procesos. Asegúrate de que cada paso se realice justo a tiempo para evitar que las tareas se detengan debido a esperas innecesarias. Esto mantendrá el flujo constante y reducirá los tiempos muertos.
- Movimiento: Diseño de Estaciones de Trabajo Eficientes Reorganiza tus estaciones de trabajo para minimizar el movimiento innecesario. Todo, desde la disposición de las herramientas hasta la ergonomía, debe estar diseñado para optimizar el flujo de trabajo y reducir el desplazamiento.
Lean como un Estilo de Vida Empresarial
Eliminar los 7 Mudas no es un trabajo de una sola vez; es una filosofía que debe integrarse en el corazón de la cultura empresarial. La mejora continua es clave, y cada pequeño cambio suma. Recuerda, Lean no es solo una metodología; es un estilo de vida empresarial que busca perfeccionar cada aspecto de la operación.
Así que, amigos, ¿están listos para deshacerse de los desperdicios y abrazar la eficiencia? ¡Lean on, leaners! La mejora continua es el camino hacia la excelencia operativa.
¡Hasta una próxima entrega!